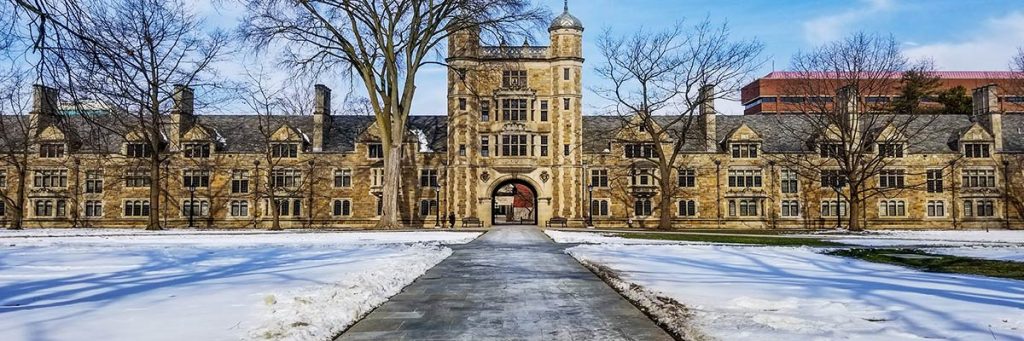
FACILITIES AND OPERATIONS WINTER MAINTENANCE SUSTAINABILITY AND BEST MANAGEMENT PRACTICES
Facilities and Operations led by Grounds Services has reduced its salt and sand use by 50% since the mid 1990’s. This milestone has been achieved by leveraging technology, using alternative materials and methods as well as additional calibration and operator training.
F&O uses liquid deicing material on sidewalks instead of the traditional granular products when the weather conditions allow. By using liquid deicing material, the crews are better able to place the proper amount of salt necessary for the conditions.
Anti-icing practices improve the level of service and reduce total salt use by applying a small amount of liquid salt to the paved surface before the storm which reduces the chance of snow and ice bonding to the pavement. This allows for better mechanical removal thus reducing deicing chemical needed. Anti-icing products are applied to paved surfaces ahead of an approaching storm when forecasts indicate there is a 50% probability of precipitation or other factors that may lead to slippery conditions for pedestrians and motorists.
Each winter storm event our crews focus on removing accumulated snow on sidewalks and plazas using equipment with plow and rotary broom attachments. Rotary brooms are the best method to mechanically remove snow and ice from pavement. The campus has over 165 miles of sidewalks to maintain with 30 designated and mapped equipment routes. Our campus is divided into 5 geographic zones. Each zone has a designated crew that has been trained on the priority locations within the zone. Once walks and plazas are cleared, the crews focus on moving snow using snow blower attachments, buckets and blades along sidewalk edges and plazas that could potentially melt and refreeze.
Alternative granular deicing products continue to be evaluated for effectiveness, non-corrosive properties, ease of application, and cost. F&O staff will use materials deemed least damaging to University facilities and the environment without compromising safety or performance.
Facilities and Operations will continue to test innovative ways to improve service as well as reduce salt use by leveraging new technology and implementing new strategies.
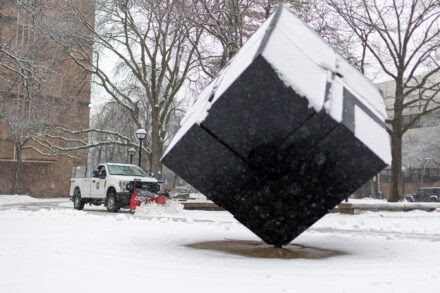
NEED SNOW REMOVAL?
Please contact the Facilities Service Center at 734-647-2059 for all snow removal requests. We will either contact you or take care of the snow removal as soon as possible.